Over the course of my Planet Exploration Project I was tasked with creating the shell of the vehicle. I was given a small list of requirements:
Lightweight, sand-tight, removeable, and strongly stick to the vehicle.
Over a couple of weeks alongside my team members, we took measurements of the powertrain of the vehicle and exported them to Onshape. After a few basic designs on the attachment mechanism to the drivetrain, we landed on velcro.
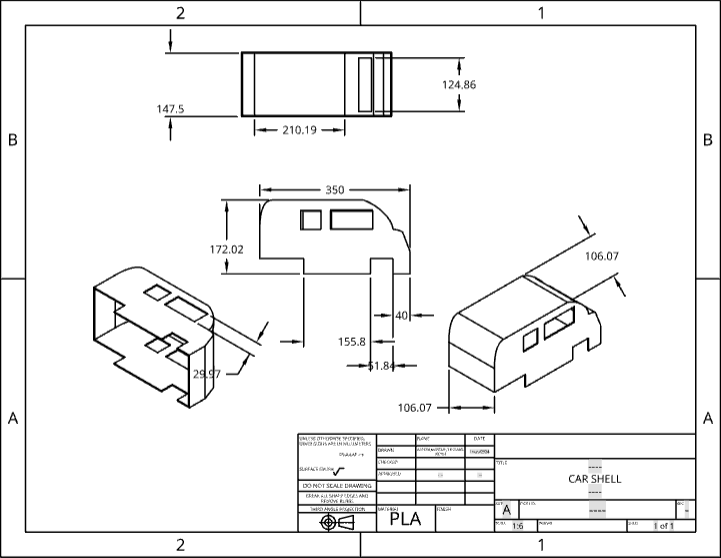
Initially, we wanted to create a van-like design to provide plenty of space for the battery and cooling systems onboard. However, this design was heavy and negatively affected the vehicles center of mass which led to unwanted tipping and reduced handling capabilities.
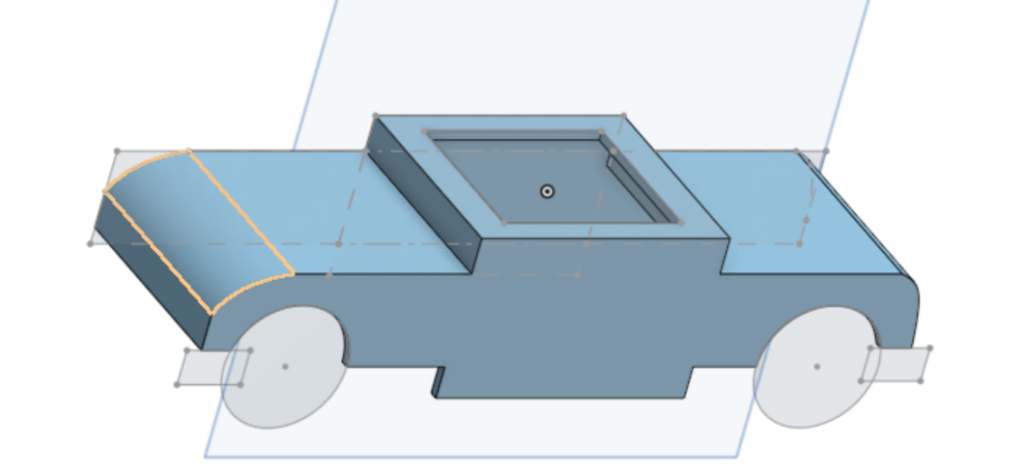
Then, we decided on a more sedan-like shape inspired by American muscle cars like the Dodge charger and the Chevvy Camaro of the 1990s-2000s
Finally, after ensuring all dimensions were compatible and snug with the “powertrain” of the vehicle, we printed it out. Finally, we attached the velcro to the shell and placed it on the vehicle. Luckily, it was a perfect fit, loose enough to be easily removable and snug enough to repel all loose sand particles.
Leave a Reply to achen27 Cancel reply