Hello all! This is the end of the Enceladus project. In this chapter, my team, Roy Zeng, Joshua Chen and me, collect data and run tests.
Abstract
Enceladus, a moon of Saturn, is one of the only places in the solar system that has the possibility of fostering life. This is the reason why my team, Beetlejuice, have decided to design a vehicle that is able to traverse its harsh terrain under these conditions:
A team of astronauts must travel a 10 kilometer round trip on Enceladus safely while combatting icy temperatures of around –201oC, geysers of water vapor, high brightness induced low visibility, dangerous radiation levels, and the possibility of escaping from Enceladus’s gravity pull (0.113 m/s2).
Our approach included extensive research, CAD design and prototyping, refer to how my team came up with a prototype of a rover for specifics. As high schoolers, we will not be able to test multiple things outlined such as the high brightness, radiation and gravity.
Vehicle
Our team had a grand plan for how our vehicle was going to look and work. However, multiple unfortunate events with printing and arduino occured, which led to major design changes, which include:
- the discarding of the suspension because of inconsistencies in printing
- the remodeling of the entire vehicle body to better suit the environment
- the annihilation of the arduino + wiring because it kept bugging for unknown reasons
Therefore, our vehicle went from this design:


to this prototype:
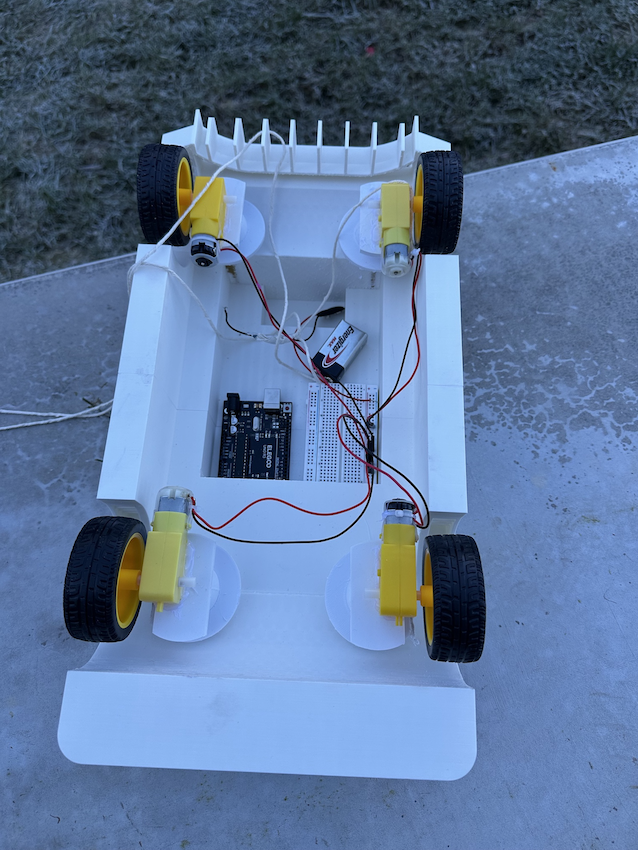
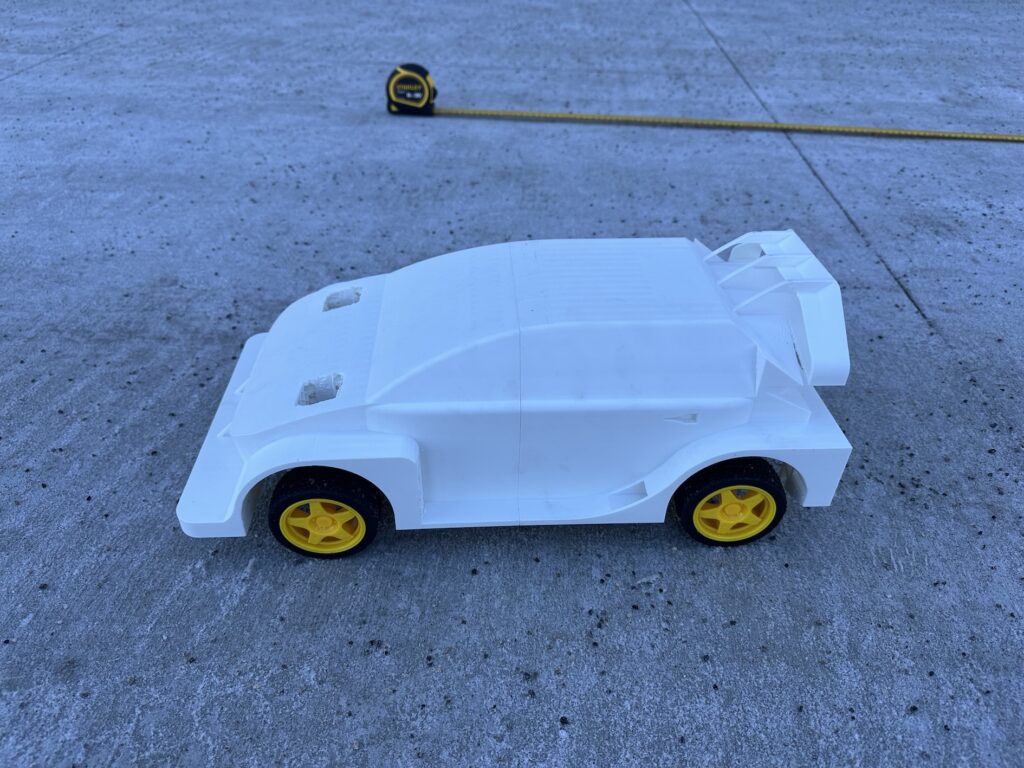
After meticulous building and 3D printing, we were finally finished with our first prototype. Shown in the images above, our car’s wiring is now a very simple circuit, as it is just a 9 volt battery connected to the motors without using the arduino or any motor drivers. In addition to all of the problems highlighted above, our car now has a string attached to stop the car (by pulling out a wire).
Testing & Analysis
Our test was initially designed to compare the vehicle on flat ground and bumpy ground:
1. Materials Needed
- Vehicle: Prototype
- Simulated Surface:
- large tarps
- small rocks/gravel/sand to create obstacles
- spray bottle
- Measurement Tools:
- camera to record vehicle/environmental interaction
2. Procedure
Setting up:
- Add small rocks between tarps to create an uneven surface.
- Create a simulated icy surface by spraying the tarp with water.
Test Runs:
- Drive the vehicle on flat ground 290 centimeters for 3 times while recording.
- Drive the vehicle through the course 290 centimeters for 3 times while recording.
- Observe how the suspension system reacts to bumps, slopes, and obstacles.
Record Observations:
- the time for the vehicle to do the course.
- areas of concern where the vehicle struggles/gets stuck
3. Analysis
- A smaller time increase on bumpy ground compared flat ground suggests better suspension performance and smoother navigation.
- A bigger time increase suggests the opposite.
Although we had no suspension, we still stuck to the plan to test the vehicle’s maneuverability. This is one of the runs from our control run on flat ground:
From this control, we realized that the vehicle was extremely slow, however, we figured that it was the low amount of voltage which could be easily increased. Other than the speed, everything was working fine. With our control, we set up our second test outside. This test did not go accordingly. I will let the video speak for itself:
This result showed many issues with our prototype. Firstly, it did not have enough battery, therefore, it could not produce enough energy/work to rotate the wheel over the bumps. Secondly, the lack of suspension made it extremely difficult for the car to handle uneven ground. Lastly, the wheels did not have enough traction. Furthermore, since we could not really collect any data, let alone any on efficiency, these tests were kind off pointless (but useful at the same time). Therefore, we devised a second test.
Testing & Analysis V2
Our new test was now going to test battery efficiency in room temperature vs cold temperature:
1. Materials Needed
- Vehicle: Prototype (two 9V batteries)
- Measurement Tools: Voltmeter
2. Procedure
- Drive the vehicle 290 centimeters 3 times in room temperature (22 °C) with battery 1.
- Test battery 1 with voltmeter
- Drive the vehicle 290 centimeters 3 times in a colder temperature (2°C) with battery 2.
- Test battery 2 with voltmeter.
3. Analysis
- Calculate voltage drop and compare them.
- If the voltage drop is similiar, then our design will fare well in colder temperatures.
- If the voltage drop is extremely different, then our design will not fare well in colder temperatures.
Our new test was now going to test battery efficiency in room temperature vs colder temperature. We did the exact same thing as before for our control using a 9.55V battery. We then moved outside, where it was around 2°C, and did the same with a 9V battery. One thing we noticed while testing is that the colder temperature also resulted in a slower vehicle, which can be seen in electric cars like Telsas.
In room temperature (22°C), the 9.55V battery dropped to 9.00V after three runs, a moderate decrease. In cold conditions (2°C) however, the 9.00V battery dropped sharply to 7.95V, a significantly higher voltage loss. To better represent this change, I have created a table:
Conditions | Initial Voltage (V) | Final Voltage (V) | Voltage Drop (V) |
Room Temperature (22°C) | 9.55V | 9V | 0.55V |
Cold Temperature (2°C) | 9V | 7.95V | 1.05V |
To quantify the battery efficiency loss, we use the formula:
For room temperature:
For cold temperature:
This indicates an efficiency loss of approximately 6% due to colder temperatures. Given that Enceladus has an average temperature of – 201°C, the battery performance would likely degrade even further in real-world conditions. Thus, we can conclude from our findings that electricity is not the optimal energy source for traveling on Enceldus.
Conclusion
To enhance the viability of our vehicle for real-world applications, several improvements must be made. The most pressing issue is power efficiency, as our tests showed a significant drop in battery voltage in colder temperatures. A solution to this would be implementing a battery heating system which could prevent extreme temperature fluctuations from affecting power output. Furthermore, we need to implement a system with more voltage so that our vehicle could run faster.
Another major drawback was the lack of a suspension system, which severely hindered maneuverability on uneven terrain. A suspension systems like the one we designed would allow the vehicle to adapt to obstacles more effectively. This would also significantly improve the comfort and safety of astronauts inside the rover, preventing excessive vibrations that could damage sensitive equipment.
Our prototype also struggled with traction, which would be even more problematic on the icy terrain of Enceladus. Future iterations should include textured or spiked wheels, similar to those used on lunar and Mars rovers.
Even with all of these changes, several issues with traversing the Enceladus surface were not addressed. These include radiation, low gravity and navigating through the many water geysers. So although we have made progress with one challenge on Enceladus, there are many left, which sheds light on how difficult extraterrestrial exploration is.
Thank you for joining us for this adventure. Beetlejuice out.
No AI was used when writing this blog post.
Leave a Reply